Primary tabs
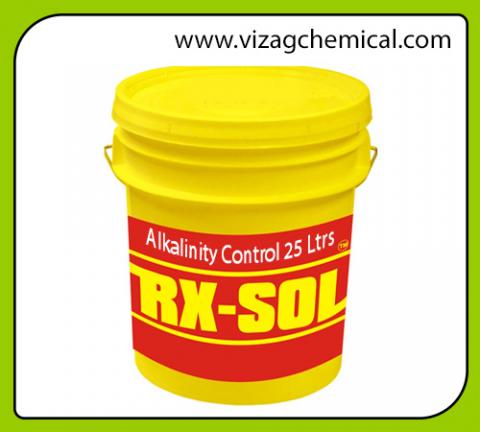
Alkalinity Control
Boiler Water Treatment Chemicals Concentrated liquid alkaline product for corrosion and Calcium scale control in boilers. Very usefull Concentrated Alkaline Liquid For Maintaining Ph - To adjust alkalinity.
Suitable for Low-pressure boiler systems (0-32 bar) , medium-pressure steam propulsion vessels (32-60 bar). And also suitable to used for high pressure steam generating systems (60-84 bar).
Mechanism : It converts calcium hardness into soft, non-adherent sludge that is easily removed by blowdown.
RXSOL-50-5002-025 provides the alkaline condition for hardness control to function correctly. Without the correct precipitation and subsequent blow down of hardness salt, scale would form. This would result in restriction in water flow, ineffective heat transfer and local corrosion. The end effect would be an inefficient boiler and ultimately component failure. RXSOL-50-5002-025 also provides the alkaline condition required for corrosion control, by neutralization of acidic gases
For optimum results dose RXSOL-50-5002-025 direct to the boiler with a RXSOL Boiler Water Treatment Dosing unit, or via the bypass pot- feeder installed in the boiler feed line.
Required dosage can be controlled by pH & alkalinity test dosage chart .
1 milliliter of RXSOL-50-5002-025 concentrated alkaline liquid per ton of distilled water provides 0.5 ppm of lkalinity hydrate.
Low-pressure boiler (up to 28 bars)
Add RXSOL-50-002-025 to 5 litre in feed – water, There is no any specific method can be passed through the recalculating or the main feed pipe into the stream or the hot well tank.
High – Pressure Boiler (28 to 60 bars)
Dissolve the desired volume of RXSOL-50-002-025 to 5 ltr of feed – water, which should then be passed into the stream or water drum through the chemical pump.
Note:- It can also be used as a neutralizing agent following acid cleaning with descaling materials ( RXSOL-11-1008--DC descaling Liq / RXSOL-54-1008-SA Safe Acid PWD )
It can also be used as a neutralizing agent following acid cleaning with descaling materials ( RXSOL-11-1008--DC descaling Liq / RXSOL-54-1008-SA Safe Acid PWD )
CHARACTERISTICS
- Alkalinity Balace mechnism to control corrosion.
- It converts calcium hardness into soft, non-adherent sludge that is easily removed by blowdown. Treated as good salt-scale controler product.
- Compatible with other BOILER chemicals
- Tested with long and continious running plant for more then 20 Years and easy to apply and use.
- Avoid contact with any acidic / oily - FAT materials.
Testing control procedure
- Test water sample from the water boiler as described in the direction of the Alkalinity Test Kit ( p & m Total ) http://www.rxmarine.com/Alkalinity-test-kit
- Determine the present alkalinity value expressed as ppm CaCO3 .
- Desired level of 100-150 ppm as CaCO3.
- A control test for the alkalinity of the water should be conducted after 3- 6 hours from the application.
The presence of alkalinity in a water sample may be due to many different substances. However, for the sake of simplicity, the presence of bicarbonate, carbonate, and hydroxide ions is commonly considered as alkalinity. The points of change in colour of phenolphthalein and methyl orange indicators, which occur at pH 8.3 and pH 4.3 provide standard reference points which are almost universally used to express alkalinity.
Very high alkalinity values can be undesirable in an industrial water supply. For example, the presence of a high methyl orange alkalinity should be avoided in boiler feed water because of the resultant carbon dioxide content of the steam. Carbon dioxide usually is responsible for the corrosion of steam and return lines. High boiler water alkalinities are also undesirable because the presence of high hydroxide ion concentration is the primary cause of caustic metal embrittlement. A very high boiler alkalinity can also lead to an undesirable carryover condition. On the other hand, the alkalinity of boiler water must be sufficiently high to protect the boiler metal against acidic corrosion and to ensure precipitation of scale-forming salts. Usual treatment approaches include setting both a minimum alkalinity level and an operating range.
Hydroxide alkalinity may be determined by adding barium chloride prior to titration to precipitate the carbonate ion from solution, allowing direct titration of the hydroxide alkalinity. Measurement of hydroxide alkalinity is also used to control lime soda softeners.
In cooling water systems, alkalinity is of major importance since the total alkalinity of a water is one factor that must be considered when predicting the tendency for the water to precipitate calcium carbonate scale. Depending on the choice of chemical treatments to protect against corrosion and scale formation, the operating alkalinity and pH ranges are chosen to balance these two features.
Alkalinity Titrimetric Method (0-200 ppm)
Principle Theory
This test is based on the determination of alkalinity by titration with standard acid to the phenolphthalein color change (or to a pH of 8.3) and to the methyl orange color change (or a pH of 4.3). For determination of hydroxide alkalinity only, barium chloride is added prior to titration to precipitate the carbonate ions. Titration is then taken only to the phenolphthalein end point. A pH meter may be used instead of the indicators to determine the end points of the titration.